What is flow wrapper?
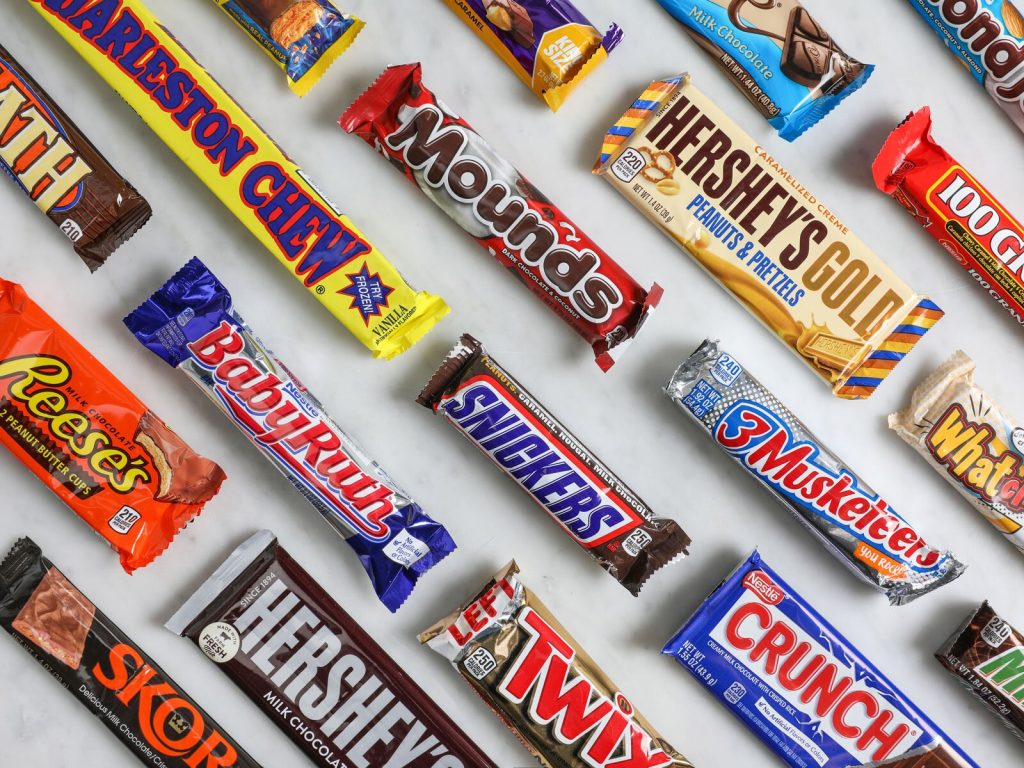
Flow wrapper is 1 of the most common packaging machine to pack foods, like candy, chocolate, wafer, cookie, bars, and other food or non-food products. It could provide good protection for products to avoid getting damaged from oxygen and moisture in the air.
How does flow wrapping work?
Flow wrap is a package with 3 sealing positions, left side sealing, sealed with cross seeing jaw; right side sealing, sealed with cross sealing jaw; and backside sealing, sealed with fin seal roller; there are 2 kinds of packing film, the hot sealing film, and cold sealing film, the difference between them is bonding methods, the hot sealing film is bonded due to the film melting with a 150℃-170℃ temperature, the cold sealing film is bonded due to the glue on the film.
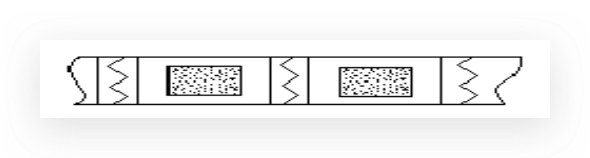
Normally, the material of the film is cpp+pet, with a thickness of 0.04-0.06mm.
Flow wrap package looks like a pillow, so it is also called pillow pack in some countries, nowadays flow wrapper is a popular machine to help food manufacturers pack their products in an efficient and stable way.
Today, we are talking about an industrial quality level, automated chocolate products flow wrapper.
OMRON solution profile of flow wrapper automation: https://automation.omron.com/en/us/industries/food-and-beverage-packaging/packaging-machine-automation-solutions/horizontal-flow-wrapper
Introduce of fully-automated flow wrapper
The automated chocolate products flow wrapper is consists of 2 sections, the feeding system, and the packaging machine.
The feedings system is a modular part that will be configured according to product characteristics, it is consists of 3 parts, the main belt, the rejection part, and the smart belt.
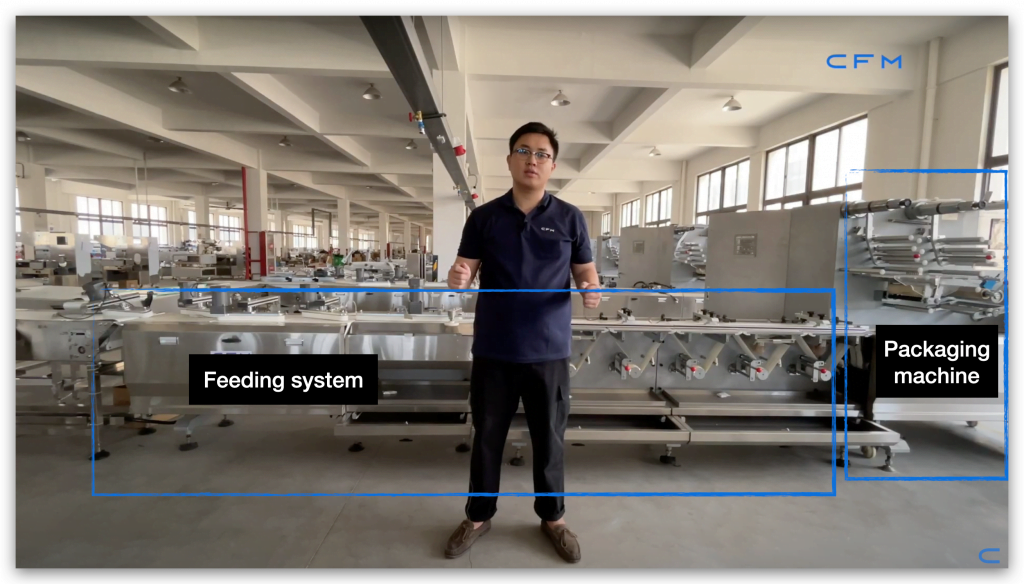
Main-belt

For the main belt, it connects with a transfer belt which connects to the production line directly to transfer the product to the main belt, in a good machine, there are some special designs to optimize the daily operating efficiency, suck like:
1) the tool-less belt tension system, belt auto-clean scraper, removable waste pan, and retractable cover, these design make the operator very easy to do the daily clean work.
2) the robust belt tracking system, makes the belt always keep running in the right direction and provides a more stable product flow.
3) Individual speed control for each belt, makes it flexible to adapt to the different products.
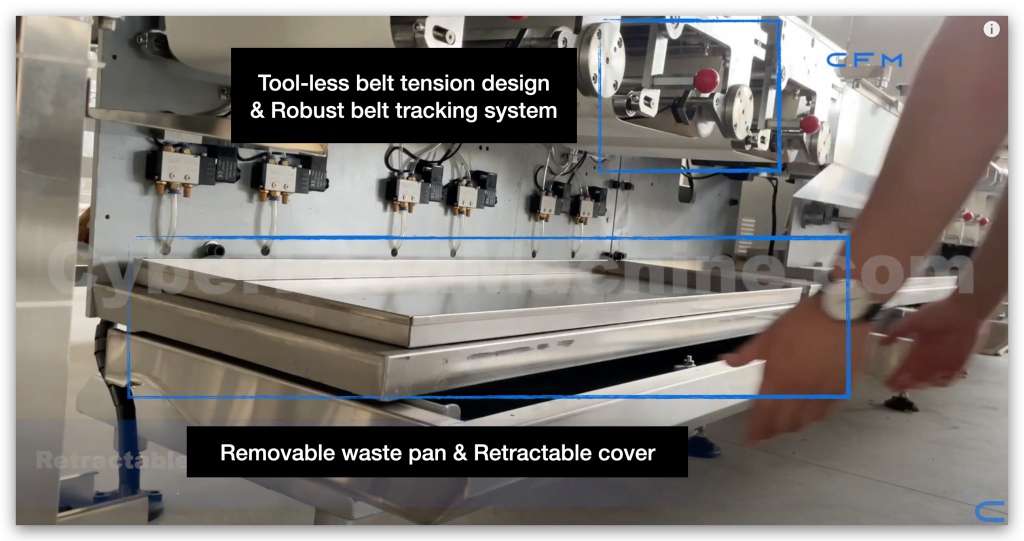
Rejection part
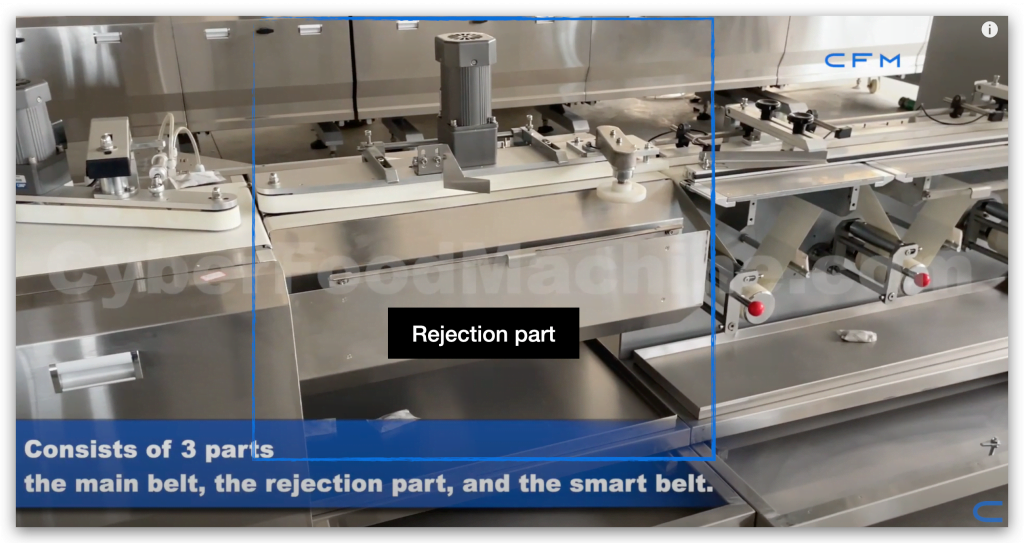
After the main belt receive the products from the transfer belt, then the machine needs to make up the products and make them as 1 line to provide a continuous products flow to the packing machine, so it is necessary to have a particular rejection part to sort out the wrong products, usually, there are 3 kinds of rejecting methods
1) Vision sensor detection, air push products; detection based on caramel image
Details extension: https://www.keyence.com/ss/products/sensor/sensorbasics/vision/info/
2) Photoelectric detection, air push products; detection based on light
Details extension: https://www.keyence.com/ss/products/sensor/sensorbasics/photoelectric/info/
3) Physical barrier, products fall off
The function of these 3 are similar to sorting out the non-ideal products, normally the first type is used in the European Flow wrapper, and the 2nd and 3rd types are used in the Chinese flow wrapper.
Smart belt

The rejection part will make all products line up one by one, then go to the smart belt, it is an ideal way to use servo motors to intelligently adjust the product’s position that could make the products flow to keep the same step with the chain and pusher pin, that means it could provide a stable and continuous products flow to the packing machine to enable high speed and precise packaging.
There are some important features for good smart belts to improve the packaging performance and operating efficiency:
1) Multi-individual belts with multi-individual servo motors.
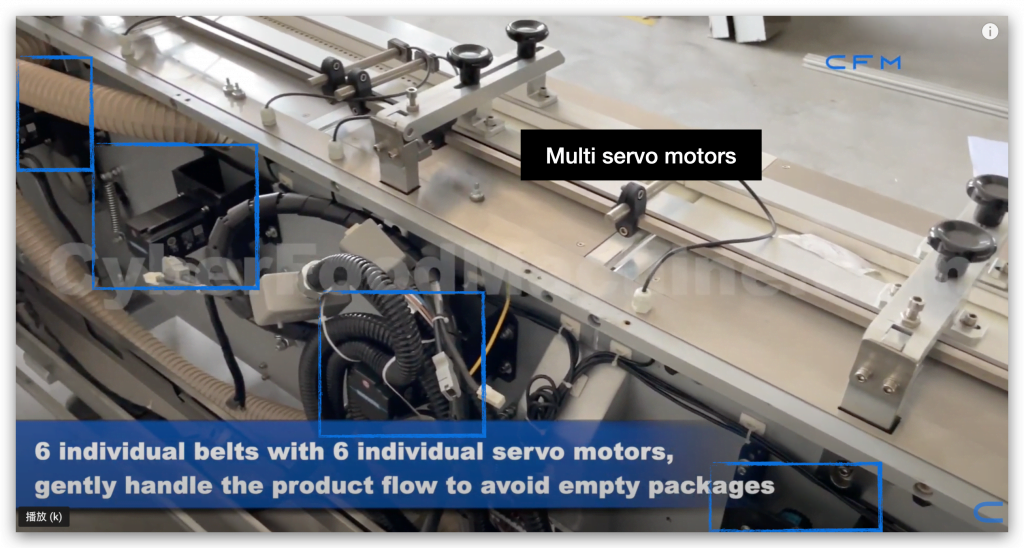
2) The good clean design, the tool-less belt tension system, belt auto-clean scraper, removable waste pan, and retractable cover, these designs help the operator very easily to do the daily clean work.
3) The alignment unit can be adjusted flexibly, this allows a very fast changeover from one format to another.
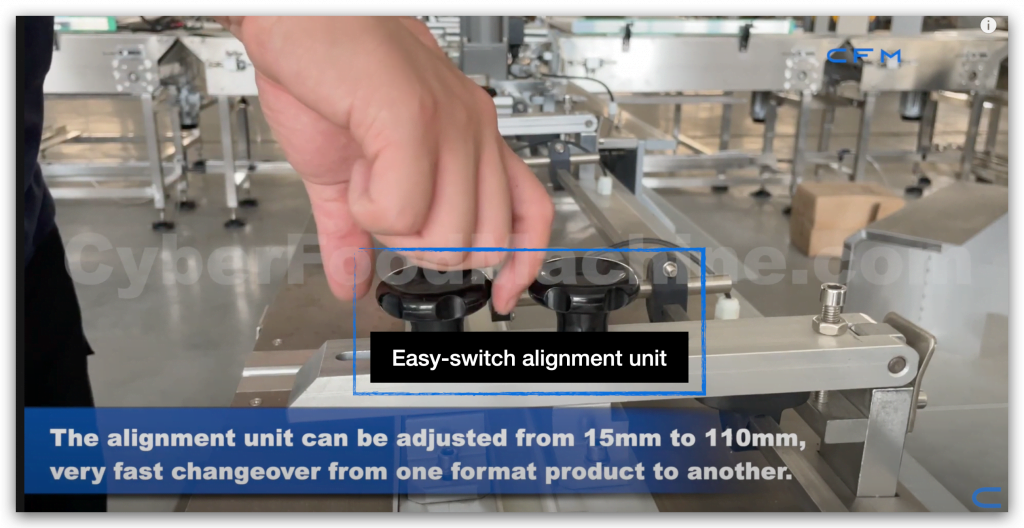
4) Punched belt with air suction machine provides a stable and smooth product flow
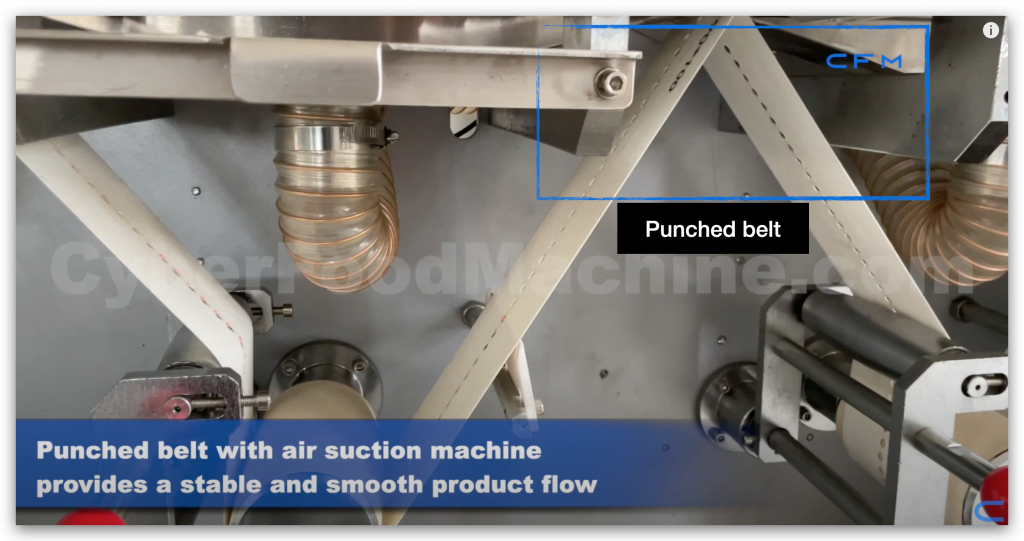
5) No product, no feed function, avoid film waste.
Packaging machine
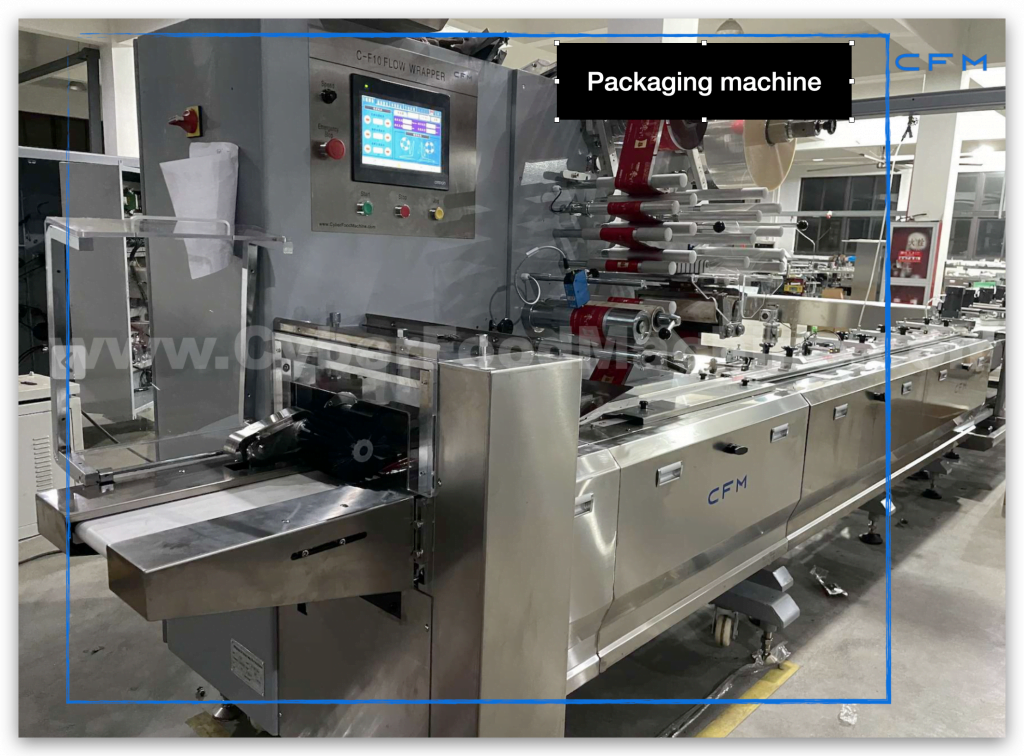
What is a good flow wrapper
1) Performance
2) Stability
3) Flexibility
Performance
For a good flow wrapper, it is necessary to have multi servo motors that could fit the above factors, firstly, let’s check out what will happen on the packaging machine for the products to come from the feeding system.
After receiving the products from the smart belts, the pusher pins, and the chain will convey the products into the film former, at the same time, the film roller will pull the film from the roll to fold the film through film former, then, the products will be tightly wrapped with the film, and go to fin roller and cross sealing jaw to create a strong package then cut onto the discharge belt and leave the machine.

So how to make all the parts run precisely? the chain, film roller, fin seal roller, cross sealing jaw? Servo motor works, 1 servo motor for the chain, 1 servo motor for film roller and fin seal roller, 1 servo motor for cross sealing jaw. With the specific programming, 3 servo motors will work correspondingly, gently handle the products and create a strong package. Also due to the characteristic of the servo motor, the operator could easily change the parameters in the touch screen to adapt for different packaging situations.
Stability
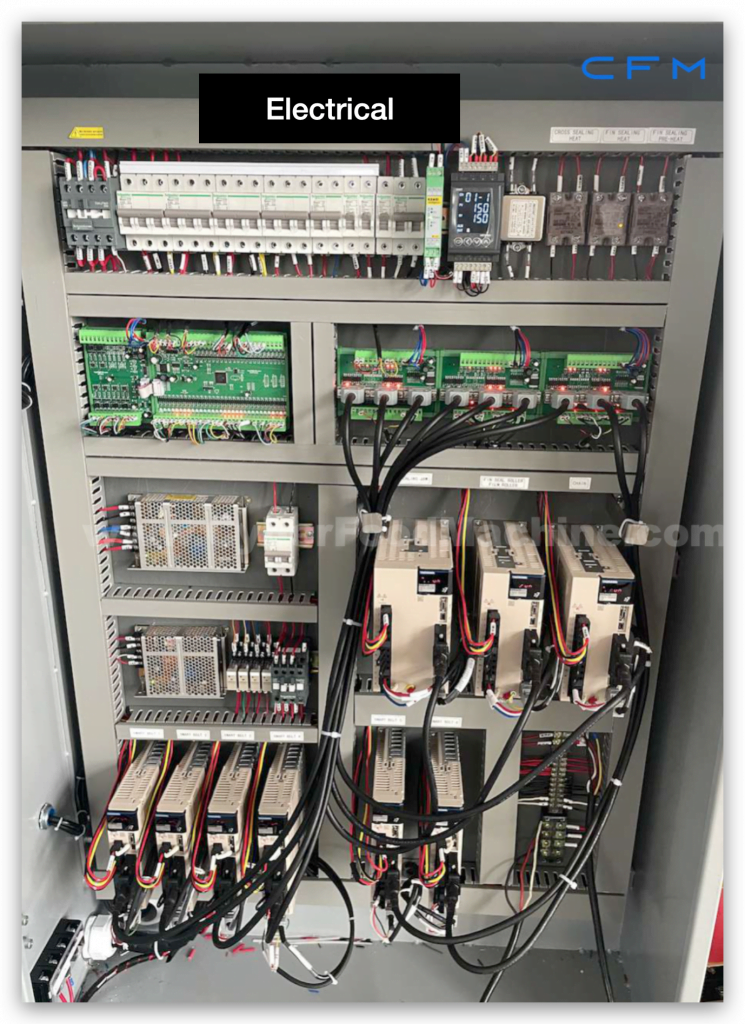
As we can see, servo motors are the key for a good flow wrapper to improve the stability and performance, in the market, there are some good brands, like Siemens, Panasonic, Yaskawa, Allen-Bradley, etc, choose the International brand, with quality assurance and good after-service. But some Chinese brand electrical like Riding and Inovance is also a cost-effective option for some customers with small budgets. Except for the electrical brand, programming is another core point for the performance, good programming could improve packaging efficiency and save waste.
For example, when film auto splicer works, there will have a connecting point of the film, and the film mark sensor need time to recheck the right position of the mark on the new film, during this period, if the machine still keeps going, there will have some waste that products in wrong packages. What could good programming do? During the working period of film auto splicer, the smart belt will stop working automatically, the extra products from the production line will be collected before the rejection parts, then only film keeps going, after the film mark sensor running in a good way, then products will be released automatically, it takes seconds.
So that’s an example of what could good programming do.
Flexibility
According to the feedback from machine users, I collect some key points design for good usability in the daily working, that’s the necessary points for a good flow wrapper.
1) Film auto splicer, film quick load design, mark auto-correct system could bring a friendly user experience and reduce the machine downtime.
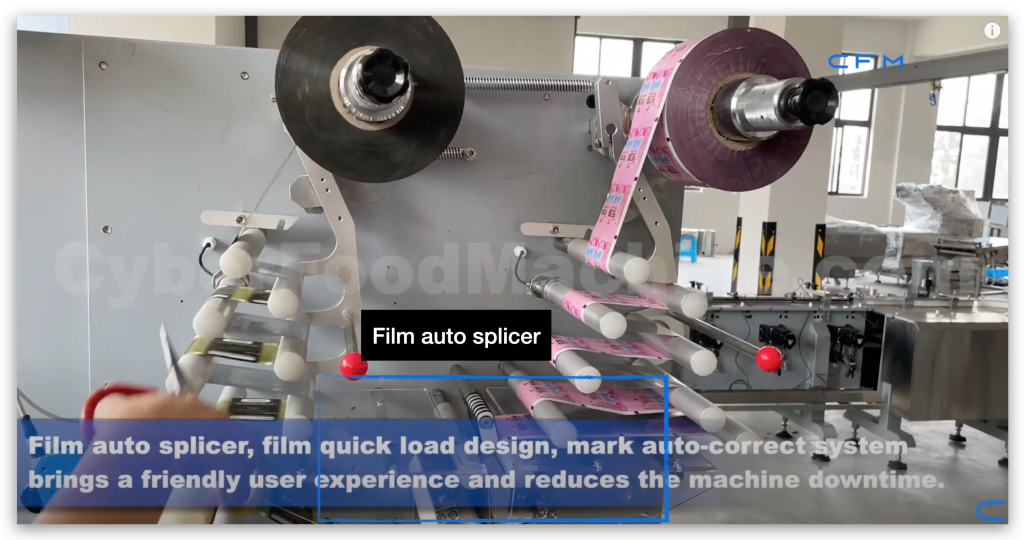
2) Distributing belt, film former, and chain have an easy exchange design that allows the operator a quick changeover and easy access for cleaning
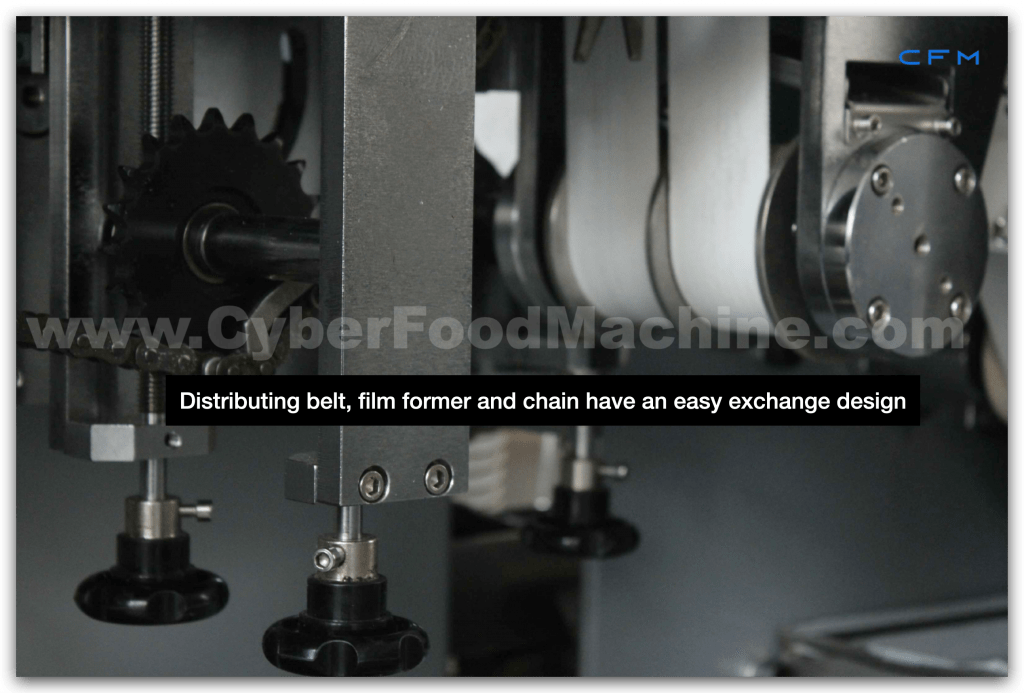
3) Easy-open fin seal cover, fin seal roller pressure easy adjustment design allows operator easy access to cleaning and maintenance.
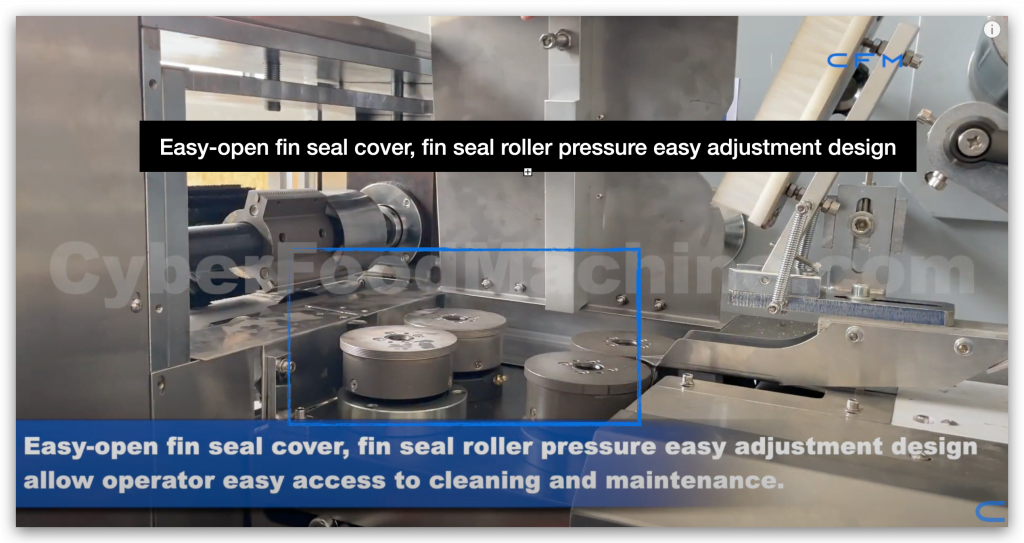
4) Film roller and fin seal roller speed radio easy adjustment design, allow operator easy adjust the film running tightness.
5) Wider cross sealing jaw design to lower the ease of maintenance, 1 example is changing the heating tube without removing the whole sealing jaw, just pull the heating tube out and change it.
6) Sealing jaw open automatically when machine stop running, prevent the film from melting
7) Brush equipped on the discharging belt, to vent the air out of the package.
8) Intuitive HMI design provides customers the full connectivity and insight into the production data.
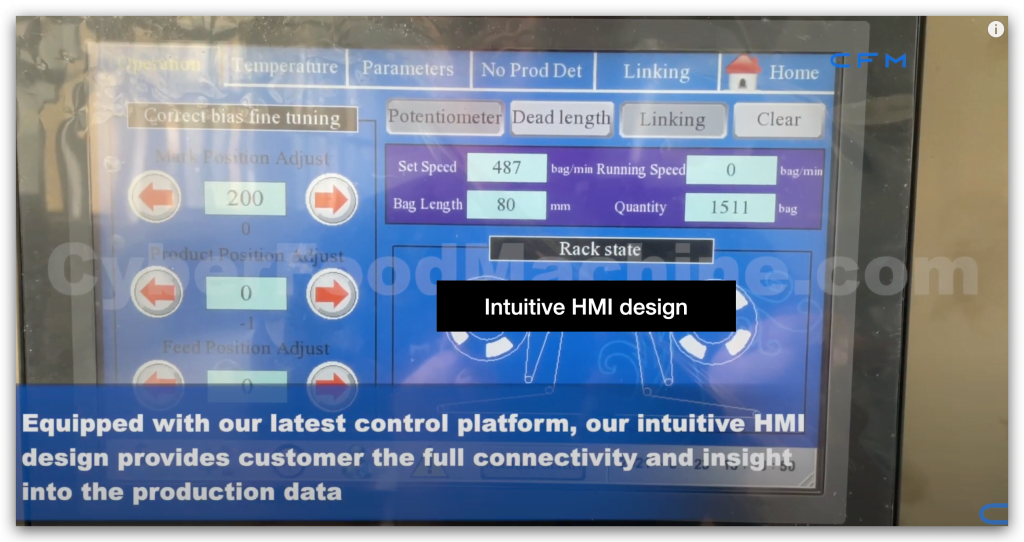
9) Products data easy switch design, let operators easily switch the product from 1 to another.
Conclusion
That’s the conclusion for what is a good chocolate flow wrapper, this type of flow wrapper also works for other products like bars, cookies, wafers, etc.
Technical review of C-F10 automatec chocloate flow wrapper: https://www.youtube.com/watch?v=T9AGbYLeVAY&t=234s